Lithium-ion batteries are a key technology in the transition from fossil fuels to renewable energies. Their large-scale use poses a number of challenges that are being met by new materials. The electrolyte (which transports Li+ ions into the battery) can be replaced by an ion-conducting solid. The "argyrodite" sulphide electrolyte can be assembled cold, but requires the battery to be kept under high pressure. These batteries are therefore always produced in the form of small pellets in a press.
Researchers at IRIG/SyMMES in collaboration with CEA-LITEN/DEHT, have taken up the challenge of manufacturing solid-state batteries by adapting conventional coating methods for liquid electrolyte batteries. Argyrodite does not tolerate humidity. In addition, the separator, usually a porous film soaked in liquid, has been replaced by a layer of argyrodite deposited on the underlying layer of active material. By fine-tuning each material and manufacturing step, the result is a battery with an NMC cathode (Lithium nickel manganese cobalt oxide LiNi0.6Mn0.2Co0.2O2) and a silicon anode (Figure 1). Silicon was chosen as the anode material instead of lithium metal, which is generally used for solid-state batteries, because it is chemically stable and can be deposited by coating.
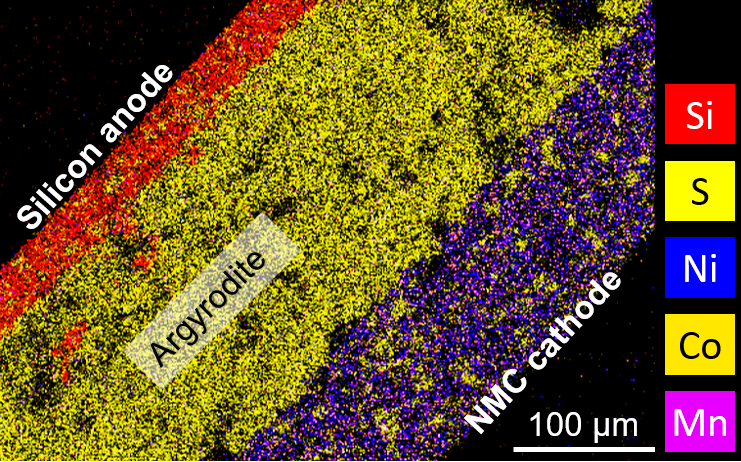
Figure 1: electron microscope image of a cross-section of the solid-state battery.
The size of these new batteries have been significantly increased from 0.4 to 10 cm2. Above all, they have improved performance as they now only need a pressure of 10 bar to withstand 150 charge/discharge cycles! This new battery format is therefore compatible with industrial production. The LITEN-IRIG team is now looking into the reasons for this mechanical stability…
Funds
FOCUS « batteries-simulation » CEA programme
Collaboration
- Pascale Chenevier IRIG/SYMMES
- Cédric Haon et Sébastien Liatard LITEN/DEHT/STB